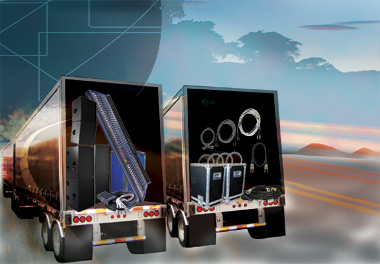
It’s a cold, gray, rainy winter day in Fort Wayne, Ind., where I’m currently stopped for a Blue Oyster Cult gig — the kind of day that sends a chill through your bones. Summer is almost four months away but it’s not too soon to start thinking ahead to the three- to four-month summer touring season. Like Santa’s workshop, SR company warehouses are cranking away with hot solder, epoxy, paint and miles of cable. The summer months are the most demanding and busy time for sound reinforcement companies that provide the gear and personnel to large touring acts, but these companies do not rest on their laurels during the “off-season.”
As Clair Bros./Showco Texas executive VP of sales, ML Procise III (who is also a six-time TEC Award nominee), explains, “Forecasting as much as a year in advance can save considerable amounts of money and avoid what we refer to as ‘crisis management.’ In the fall of 2006, we started, and continually update, the company-wide sales forecast driving into the new year with a focus on equipment and human resources required to service our global client base. We concentrate our efforts on ramping up during the summer ‘peak season’ months, solving conflicts, and creating build and purchase schedules. We have a very strong staff in each of our global shops to handle maintenance issues, updates and upgrades; that staff strengthens in numbers during the summer months. We also address these issues by trying to deploy as many projects from the main home office/shop to keep quality control under close observation. This goes hand-in-hand with equipment update of, for example, digital console software.”
While Procise cites digital consoles as an example, many other sound companies are pointing to these in-demand boards as an integral detail of their forecasts. Jack Boessneck, executive VP at Eighth Day Sound (Highland Heights, Ohio), “hasn’t purchased an analog desk in four years. We get requests for the [Midas] XL4 and I have multiple XL4s out now, but I won’t buy any more of them.” Digital consoles facilitate festivals — most-often seen during these peak months — where multiple bands perform on the same stage. In the past, there was a need for multiple analog desks to speed changeover between performers, but digital desks eliminate that requirement, providing prebuilt scenes for each band. “Sending out two digital consoles is much easier than four analog desks with multiple patching harnesses,” reveals Paul Owen, VP at Thunder Audio (Taylor, Mich.). “The prep time on an analog system is very time-consuming. I find that if all of the engineers are ‘on the same page’ and we give them one digital console, then no one complains. If you tell engineers that it’s a [Yamaha] PM5D, a DiGiCo D5 or Digidesign VENUE, they are more than happy to bring their own key [i.e., memory stick]. You’ll find on the festival circuits — especially in Europe — that a lot of engineers will walk in with their key, whereas in an analog situation, they’d be carrying a rack with effects, gates, comps and cables.”
In some cases, a sound company will ask for an engineer’s input list or mixer configuration file well-before the summer festival months, enabling the desk to be ready on-site.
Although digital desks are all the rage, many engineers are still chasing the analog sound. “I find a lot of engineers asking for boutique studio tube compressors and preamps to make their digital console sound analog,” says Frank Provenzano, CEO of Pro Sho Sound Inc. (Staten Island, N.Y.). “There’s a place for digital consoles due to footprint, truck pack and setup time, but sonically, a Heritage 3000 is superior. Maybe I’m just an analog guy in a digital world.”
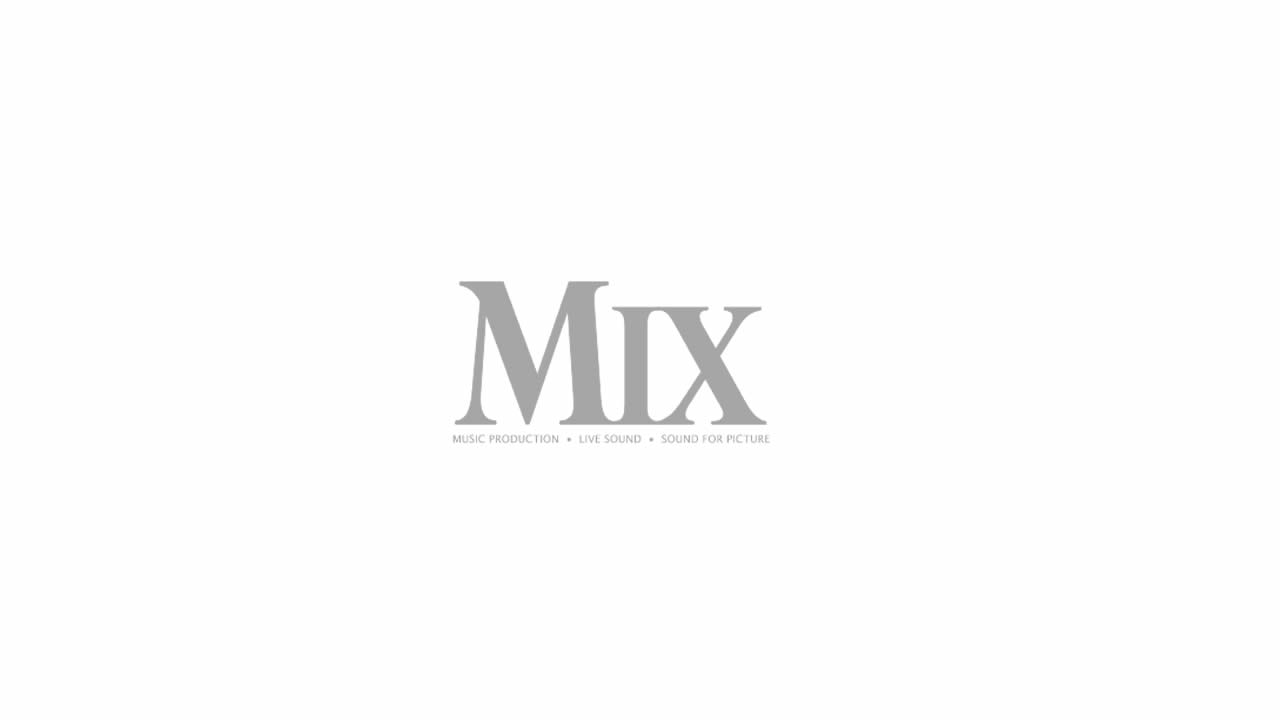
ML Procise III of Showco
Albert Lecesse of Audio Analysts (Colorado Springs, Colo.) agrees: “There is always what I call the analog ‘money channel.’ Whether for the lead singer or the lead guitar player, there are always one or two channels of premium studio-level processing, like a Crane Song limiter and Avalon mic pre. In any case, we use a multicable system that is pretty much universal for our systems. What changes is what is inside the rack — connection to the console is via multipin. It’s very quick to get up and running. We have certain prebuilt racks such as amp racks, drive racks and even computer racks — we have to be IT [information technology] people, too, nowadays. Then we have what I call the ‘flexible stuff,’ like two Avalon pre’s with a Neve compressor inserted to a PM-5D. That kind of gear gets examined on the component level — the individual mic pre or compressor is tested — then it gets racked up with its multipin interconnect. Then it’s tested at the rack level by another person and goes out to the loading dock where we have a separate area called the system test area. That is where we bring all the effect racks, the amp racks, the consoles, the snakes and hook them up to one set of cabinets for stage-left, one set for stage-right and one subwoofer. I don’t hook up all 72 cabs to test the electronics. [Laughs] We make sure that everything works as it should, because when you are doing one-offs [such as in a festival situation], you want to show up with pre-programmed templates. Once that gear has been tested, it can be packed into a truck.”
“When we send a tour out, we send spare cables, connectors, amps, drivers — the whole nine yards,” stresses Owen. “That makes it easier on the crew who are out in the field with the system. We have been using the Meyer MILO line array, and it has built-in, modular amplification, so you can easily swap out an amp. Some people shy away from powered monitors and line arrays, thinking, ‘What if you have a failure?’ We have been very fortunate in that we really haven’t had any failures during a show.”
MAINTENANCE BEFORE GETTING ON THE TRUCK
Maintenance and upgrades are at the top of any sound company’s off-season to-do list. Unfortunately, the workload doesn’t wait for refits. “Upgrades are always done on a watched, controlled basis,” explains Boessneck. “You can’t just go ahead and say, ‘Yeah, we’re going to change all the amp racks,’ because they are never all here, so we retrofit on a gradual rolling basis. Gear comes back to the shop, we retrofit it and run it back out.”
For Jon Monson, systems coordinator at Rat Sound (Oxnard, Calif.), “Maintenance is a constant process. We work hard all year on this task. Every year, we make a list of company-wide upgrades to perform in December and January. We call it our ‘December List.’ It involves less maintenance and more upgrade or exchange. For example, we have some cabinets still on EP connectors and we’re changing them all to NL. This isn’t really maintenance as the cabinets with the EPs work fine, but we want to standardize things. Unfortunately, this is getting more challenging as we have become busier year-round. We also try to do inventory in those months to reconcile what’s in the computer with what we actually have on hand, which is also getting tougher when we have several large tours out over this period.”
In the touring world, gear that doesn’t work is unacceptable, and everyone has a routine for evaluating gear returned from the road. “Once a year, all of our chain motors get re-certified,” reveals Lecesse. “I have a few guys on staff who are CM hoist-trained. We keep a meticulous record of when they were last tested. We do a load test every year, look at the cable connectors and so forth. Same thing with the rigging: If a piece is bent or choked, we replace it with new material. That concept goes down the line even to mic stands, which are almost consumables to us. They get taken apart and put back together constantly. Turning them over is a great source of used gear for the local bands here, and there’s a little bit of recycling involved. They look a little ratty for me, but they are fine for a young band starting up.
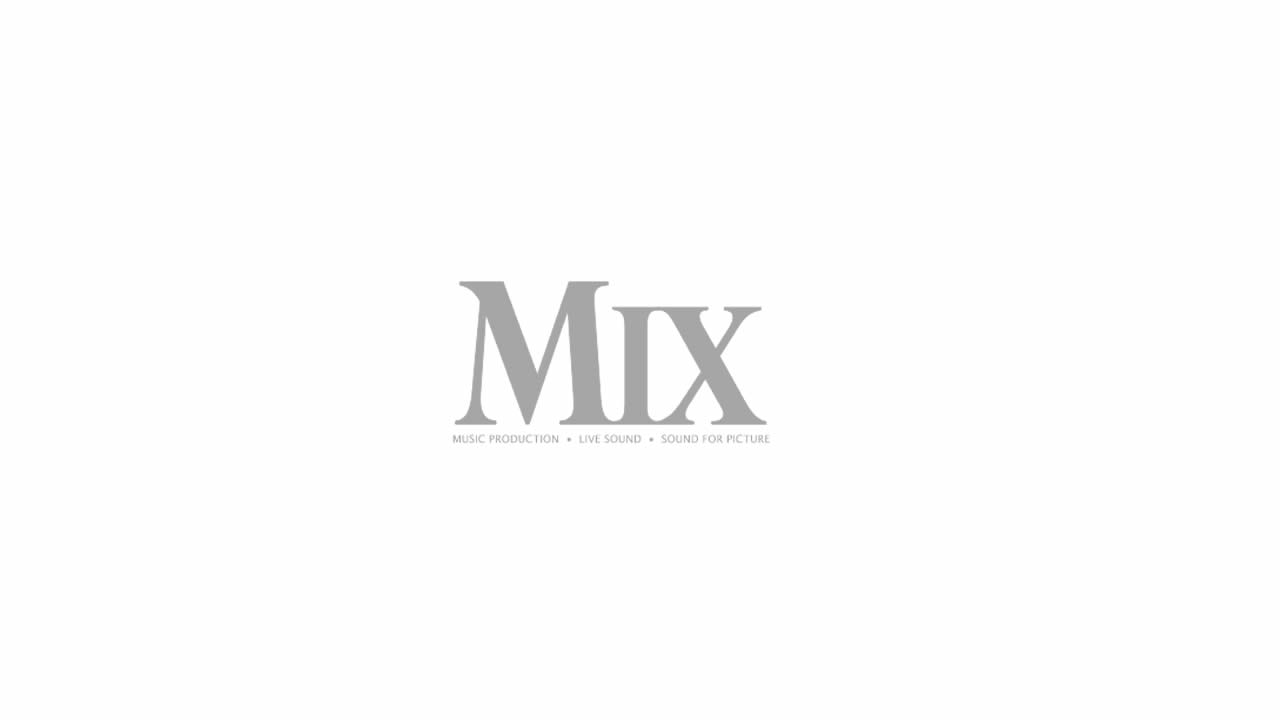
Thunder Audio’s Paul Owen with Metallica’s James Hetfield
“Concurrently, I have two people whose full-time job is basically to sweep, buzz and rattle-test every single loudspeaker when it comes back,” Lecesse continues. “For microphones, I built a small booth about the size of a broom closet. It has an EQ’d speaker on the bottom and an SPL meter with a standard calibration mic. Then we have pre-saved curves in [SIA] Smaart for various microphones. When we need to test 27 [Shure] SM58s, we load the difference trace, compare the response of the microphone to the standard curve and look for gross frequency response changes.”
“Rather than wait for a new order to be pulled and checked, we check all outboard dynamics, effects, playback and record equipment upon return from a project,” Procise says. “After it’s checked, it can be put on the shelf, ready for the next project. When board groups are assembled, those individual pieces are checked with the entire console group connected. We maintain a tremendous amount of inventory of all types of equipment and have sophisticated testing systems for mics, cabling, amps, speakers, et cetera. We rely on road reports from staff and independent engineers on equipment performance. The only real measure of road-worthiness and application is by the acceptance and specification by the touring road engineers.”
Provenzano agrees, stating, “All of our production managers have a gig sheet that they hand in at the end of their event with necessary equipment or truck repairs that need to be made. This is checked first, so any gear that is malfunctioning can be red-flagged and sent to the bench before it ends up on another event. We try to maintain good relationships with other production companies in our area and even some of our clients, making it easy to get gear in a pinch.”
Rat Sound evaluates all of its loudspeakers “with tone sweeps and noise, and for polarity issues,” notes Monson. “Wedges are also tested with voice, because problems can pass all the other tests and only show up when the monitor engineer starts talking into the wedge — and that’s the first thing a monitor engineer does on a one-off or the first day of a tour. In my opinion, you’d better test your wedges in the shop with voice to make sure there are no audible issues. You don’t get a second chance to make a first impression.”
Boessneck tests Eighth Day’s loudspeaker components “the minute they come back. Everything we have in our inventory is tested and ready for the road. It’s the same with everything else, even something as simple as cleaning the amp racks. If it’s been on the road for six months, you’d better clean it out because God knows what’s in there. [Laughs]
LOAD IT UP
With increased fuel costs (which typically sky-rocket during the summer months), one of the issues addressed by Provenzano is the truck pack. “All of our smaller speakers that in years past have been in covers are now getting road cases. Along with that, we are streamlining our case designs across the board so that we can facilitate a better truck pack. With everything in an ATA case, storage at a lot of our events — especially corporates in hotel ballrooms — is becoming an issue. We find that more often we have to load out our ‘deads’ back into the truck, which costs us time, labor and money. So streamlining our truck packs is just another little way we can become more efficient as a company.”
Procise’s view of road work sums it up well: “No matter what equipment you’re talking about, there is only one topic of concern for a road company: How to make it more road-worthy. It’s a never-ending quest.”
In addition to being Mix’s sound reinforcement editor, Steve La Cerra mixes front of house for Blue Oyster Cult.