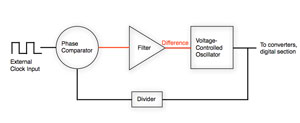
Fig. 1: The block diagram for a traditional phase-locked loop circuit, or PLL.
Good timing is the difference between salad and compost. As in most things in life, timing is critical to success. In digital audio systems, it’s what makes audio sound pristine instead of like garbage. Multiple pieces of interconnected digital gear must operate in perfect synchrony to produce great results.
This month, Mix looks at the linchpins for synchronizing digital-audio systems for music production: master clocks and clock-distribution boxes. We’ll discuss what these devices do and how they (sometimes) differ. We’ll examine why rock-solid clocking is so crucial to producing high-quality sound and how manufacturers incorporate innovative designs to improve the quality and reliability of their clocks. Our journey begins with a look at the heart of most digital clocks: the humble crystal.
GOOD VIBRATIONS
In order to transduce and transmit audio properly, a digital audio device uses an internal clock that regulates the rate of flow—the sampling frequency—of digital 1s and 0s in its bitstream. The clock typically uses a crystal that physically vibrates when excited by an electric current. At the factory that supplies pro-audio manufacturers with these crystals, the size and shape of each is tweaked to make it oscillate at a very specific frequency. Interestingly, this frequency is way higher than what is ultimately desired for use in digital audio; a multiplier divides it to yield one of the nominal sampling frequencies used in production.
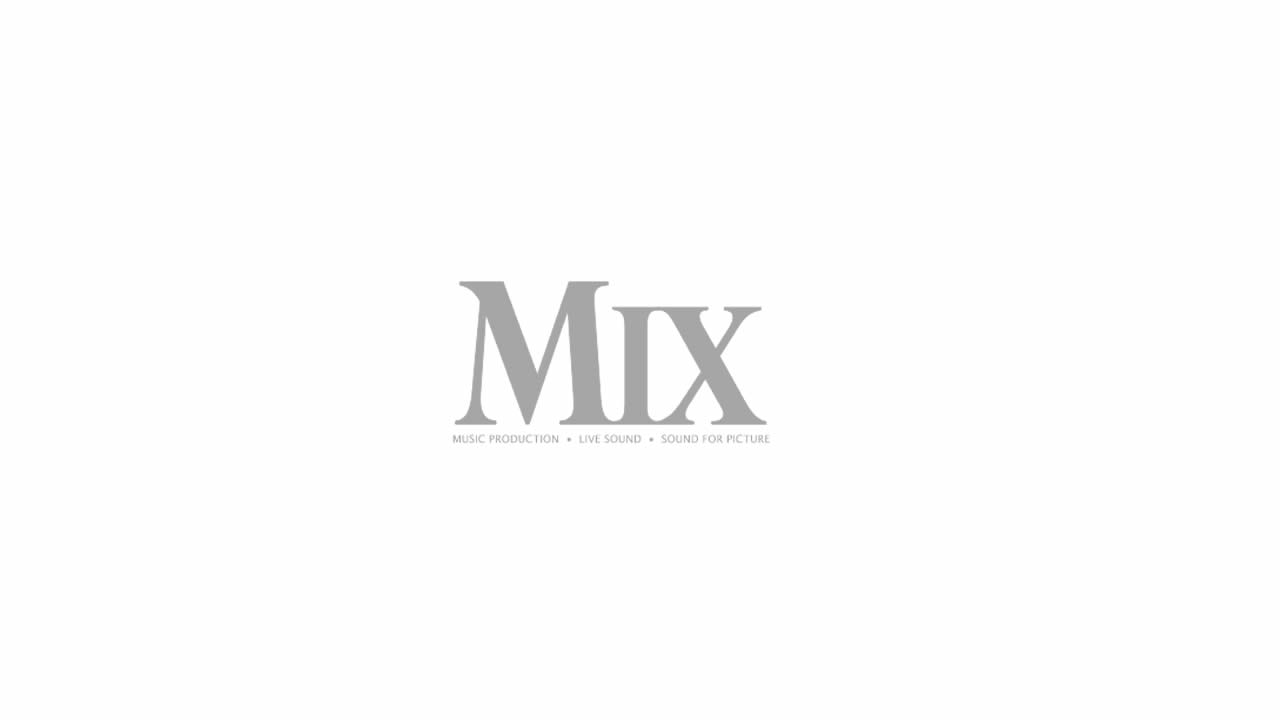
All current Lynx converters use a hybrid PLL circuit called SynchroLock, together with an analog PLL, to reduce jitter in external clock signals. The Lynx Hilo converter is shown here.
For example, converters made by Lynx Studio Technology include crystals that oscillate at 11.2896 MHz, which rate is then divided by 256 to achieve the nominal sampling rate of 44.1 kHz. Crystal-based clocks that operate at various sampling frequencies need a separate crystal oscillator for each base frequency: 44.1 kHz and 48 kHz. The crystals do double-duty to also produce sampling frequencies that are multiples of 44.1 and 48 kHz.
The rate at which these crystals vibrate is quite precise, although not exactly the same from one crystal to another. Bob Bauman, co-founder and chief hardware engineer for Lynx, elaborates: “Crystal oscillators are spec’d for drift over temperature and time. You can get very accurate oscillators that will drift over 0 to 70 degrees Celsius only five parts per million or lower.” To further increase the stability of their crystal-based clocks, some manufacturers use an oven to keep the crystal heated to a constant temperature. “Oven-controlled oscillators are the most accurate,” says Bauman. “By maintaining the [crystal’s] temperature, you maintain the [clock’s] frequency to phenomenal tolerance.”
Phenomenal, but not zero. Every clock is subject to some drift away from its nominal frequency due to aging of the crystal and other factors. This causes huge problems when you hook up multiple digital audio boxes together and attempt to operate them all using their internal clocks, none of which exactly match the others in frequency. All the pieces in a digital-audio system—stand-alone A/D and D/A converters, I/O boxes, mixers, signal processors and so on—must operate at exactly the same sampling frequency from moment to moment, or the system will quickly fail to pass audio. (The time to failure depends on the quality of each clock.)
In addition to frequency drift, every clock is subject to some amount of jitter, or short-term deviations from the nominal sampling frequency. Put another way, jitter is fluctuation in the time interval between successive pairs of samples in the bitstream. The inconsistency in sampling intervals causes distortion in the shape of the resulting waveform.
High amounts of jitter can cause audible clicks and pops in the audio path. But even a tiny amount of jitter affects audio quality: The soundstage for stereo tracks narrows, localization in the stereo field becomes vague, bass instruments sound flabby and unfocused, high frequencies sound harsh and glassy, and the overall sound becomes slightly veiled. As jitter is reduced, clarity improves, highs sound sweeter, the bottom end tightens up, the soundstage widens and imaging trends toward pinpoint accuracy.
TRADITIONAL SOLUTIONS
To reduce jitter and prevent loss of lock due to clock-frequency drift, every digital audio device in an integrated system should synchronize its internal clock to the same reference—a master clock. The master clock can be generated by any box (such as an A/D converter) in your system, but you must designate one and only one clock as master in order for the system to work. It pays to select the master clock wisely. The less jitter the master clock produces, the better the sound quality will be for your productions.
The way in which the master clock is distributed throughout your digital-audio system also affects the amount of jitter generated. The flakiest setup is to use the word clock output—or alternatively an unused AES/EBU or S/PDIF output—on your designated master device to route clock from one digital box to another in series throughout your system. (AES/EBU and S/PDIF bitstreams contain word clock embedded in their audio data; their interfaces can use the embedded clock just like dedicated word-clock connections do to synchronize another digital device, even when outputting only digital black [no audio].)
Daisychaining word clock from one device to another causes a progressive accumulation of jitter with each box the clock signal passes through. A better solution is to use a clock-distribution box—a master clock with multiple outputs powered by built-in distribution amps—to deliver clock signals directly and discretely to each box in the system in a star configuration. Antelope Audio, Apogee Electronics, Black Lion Audio and Drawmer are a few of the companies that make clock distributors.
Each box in a digital audio system synchronizes to the master clock using an ingenious circuit variously called a phase-locked loop or phase lock loop (PLL; see Fig. 1). Inside the PLL, a voltage-controlled oscillator supersedes the crystal in generating clock signal whenever the box is switched to external sync; the VCO-generated clock drives the box’s internal digital circuitry and converters. The VCO tries to match its clock’s phase to that of the incoming master clock by locking to every edge of the word clock’s square wave. It does this by looping its output back to a phase comparator that’s placed before the VCO in the PLL circuit.
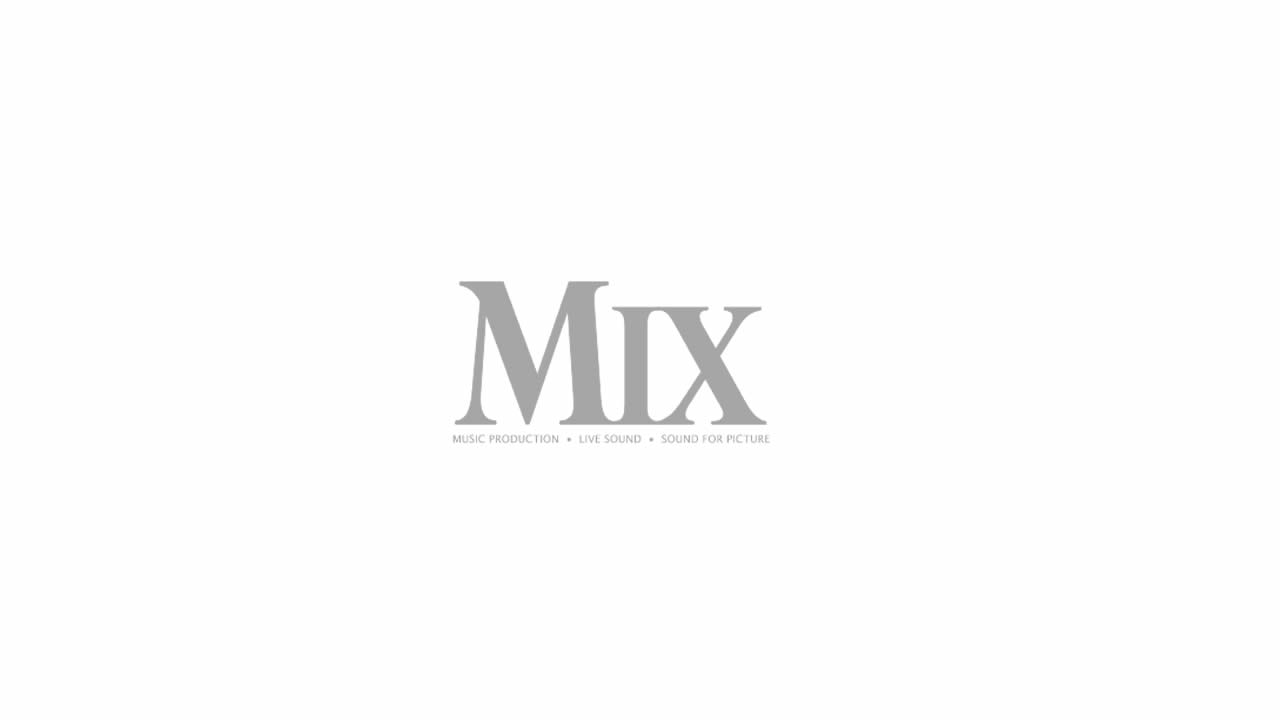
The C777 clock in Apogee’s Big Ben Master Digital Clock executes many of the traditional PLL’s functions in DSP, attenuating jitter and increasing tolerance of clock-frequency drift.
According to Roger Robindoré, Director of Product Evangelism at Apogee Electronics, the PLL’s phase comparator “creates a voltage based on the phase and frequency difference between the oscillator’s looped-back output and the external clock input.” This so-called difference voltage tells the VCO whether to speed up or slow down on an ongoing basis in order to minimize the phase difference between the clock it generates and incoming master clock. But there’s a twist: In order to keep the VCO from reproducing and thereby propagating any jitter in this difference voltage, traditional PLLs use a lowpass filter to slow down the rate of voltage change. While this VCO design effectively attenuates jitter, it’s also less capable of locking to an external clock that deviates a lot from the nominal sampling rate, either due to quality degradation or practical applications such as varispeed or video pull-up/pull-down. Loss of lock can cause audible dropouts.
NEW DESIGNS
To address the traditional PLL’s tradeoff between jitter attenuation and the ability to lock to a wide range of external clock frequencies, Apogee dreamt up an innovative clock design.
The Apogee C777 clock—used in the company’s Big Ben, X-Series and Symphony I/O—substitutes a Direct Digital Synthesizer for the traditional PLL’s analog VCO. The DDS constructs a sine wave in the digital domain, basing its frequency on that for an external clock signal; the DDS can accept a wide range of sampling rates. A crystal governs the rate at which this sine wave is assembled and then converted to the analog square wave needed for clocking; since a crystal controls this process, the result is a low-jitter clock. Apogee states that because the DDS is a digital circuit, there is “no analog over/under-shoot or settling time, no component aging or temperature drift.”
The C777 clock also uses Apogee’s DSP-based Adaptive Loop Filter, which dynamically adapts to external clock in the digital domain. Unlike with an analog LPF, the ALF can loosen its action to maintain lock when the quality of inputted external clock is degraded. Afterward, when the external clock’s quality improves, the ALF can tighten its action to keep jitter to a minimum. In this way, the C777 dynamically addresses both jitter and clock-frequency tolerance.
Antelope Audio takes a very different tack in addressing both clock-frequency drift and jitter. Their Isochrone 10M Rubidium Atomic Reference Generator serves as an uber-master for their crystal oscillator-based master clocks (which include the company’s OCX, Trinity, Eclipse and Orion). According to Marcel James, Antelope’s North American Dealer Representative, the 10M’s purpose is “to give you an ultra-stable source rate for our other (crystal-based) clocking products that overrides (their) crystals.”
James contends that even the very best crystal oscillators (including oven-controlled ones) will drift by one sample per second. Two synchronized atomic clocks, on the other hand, “will remain sample-accurate for eight days,” he says. “It’s a hundred-thousand times more stable.” All of Antelope’s crystal-based clocks can connect to the 10M, and their crystals are oven-controlled.
Instead of exciting a crystal, the 10M resonates rubidium gas, an atomic element, with a radio frequency operating at a 10MHz rate. James says the 10MHz rate is used because it is easily divisible when converting to one of the nominal sampling rates used for digital audio. He casts the 10M as an optional upgrade to Antelope’s master clocks and converters, which many users operate without the 10M. He maintains that all clocks should ideally include an atomic clock circuit, but he recognizes its high cost is prohibitive for many users.
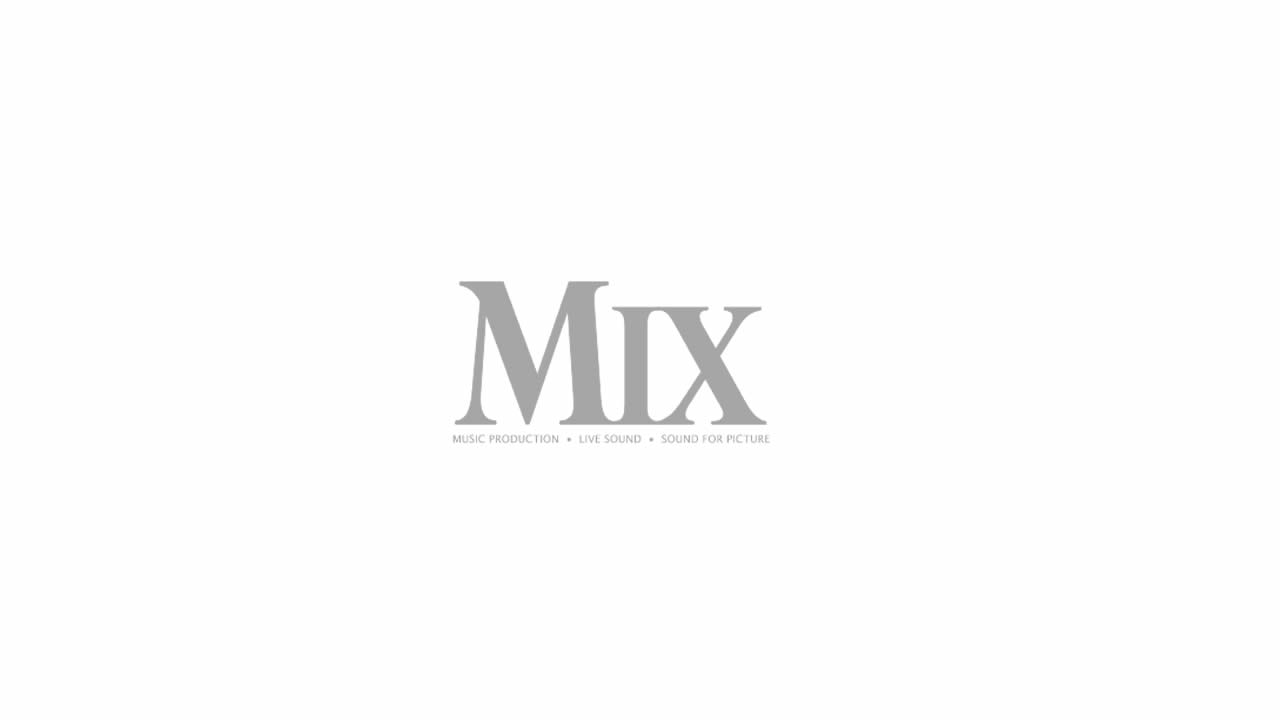
Antelope Audio’s Isochrone 10M Rubidium Atomic Reference Generator is an optional master synchronizer for the company’s crystal oscillator-based master clocks.
The 10M’s matching transformer extends the maximum cable run for word clock roughly ten-fold—to around 150 feet—using standard word-clock cable. That makes the 10M a compelling solution for synchronizing master clocks and converters throughout a multi-room facility.
Antelope also differentiates their products by deliberately incorporating random jitter in their core technology. “Some jitter is good,” James asserts. “We like some distortion in our audio. Once we remove the jitter, we actually induce small amounts of controlled jitter in our jitter-management module that resides in our crystal-based clock. We’re talking about really carefully calculated, randomized jitter. This is done to humanize the digital chips used for the conversion process, to make them sound more natural.”
NOT EVERYONE AGREES
From Lynx’s perspective, companies that use atomic clocks in their designs place undue emphasis on controlling frequency drift over the long haul, when they should be concerned about how much drift there is from sample to sample. “Atomic clocks are very good at long-term accuracy,” Lynx’s Bauman allows. “The problem is they’re not very good at sample-rate period time. They don’t have great jitter specs. In clocking in A/D and D/A converters, the most important thing is we want as low jitter as possible to reduce artifacts in the conversion process. You don’t have to have that good a clock [simply] to lock a bunch of equipment together.”
Bauman also disputes that using an external master clock to synchronize converters will necessarily make them sound better. “If that’s the case,” Bauman asserts, “the clock-generation system inside the A/D or D/A converter was not designed correctly in the first place. A [external] clock can change the sound of your converter, but in our case it always makes it worse, in terms of accuracy of conversion. You are adding distortion artifacts, some non-harmonic. But I don’t discount the fact that some people may like that [sound] better.”
Antelope’s James rebuts Bauman’s argument that an internal clock will outperform one driven externally. He attributes this to the box not being able to properly follow external sync: “The benefit of a very well-designed clock outweighs the disadvantages of having to clock externally, in most cases. There’s one main caveat: Does the re-synthesis of the [slave’s] circuit itself ignore a jitter imprint? There are some converters that de-jitter anything coming in, which can ignore some of the benefits that our clocking has.”
Bauman also questions the accuracy of Apogee’s DDS. (Lynx uses in all their recent products an analog PLL for very fast locking, followed by a hybrid PLL scheme called SynchroLock that generates a low-jitter clock.) He argues that because DDS synthesizes the different nominal sampling rates, arithmetic errors in that process—along with jitter inherent in the attendant crystal oscillator—create greater total jitter than what a crystal would produce on its own. Apogee’s Robindoré acknowledges the theoretical potential for arithmetic errors to occur in digital synthesis but asserts the C777’s rigorous engineering precludes them from arising.
HEAR FOR YOURSELF
Detractors of synching externally to a master clock maintain that attempting to generate phase-locked clock signal using the VCO in a PLL will always create more jitter than using an internal crystal would. And, they argue, the PLL will filter out any benefit bestowed by a superior external clock in the first place.
But let’s face it, if you have multiple digital devices in your system, all but one must be externally synched to a designated master in order for the system to work. And not all converters—especially those used in garden-variety I/O boxes—sound good even when using their internal clock. In many cases, a rock-solid clock distributor can make a dramatic improvement in the sound of a digital system. I’ve heard it.
There are many other factors besides what’s been presented here that go into making a terrific-sounding master clock, including the device’s analog circuitry and power supply. In the end, the best strategy for potential buyers is to set up a blindfold-listening test of clocks made by different manufacturers—including boxes you already own—and select which one sounds best. Let your ears be your guide.
Mix contributing editor Michael Cooper is a recording, mix, mastering and post-production engineer and the owner of Michael Cooper Recording in Sisters, Ore.